History
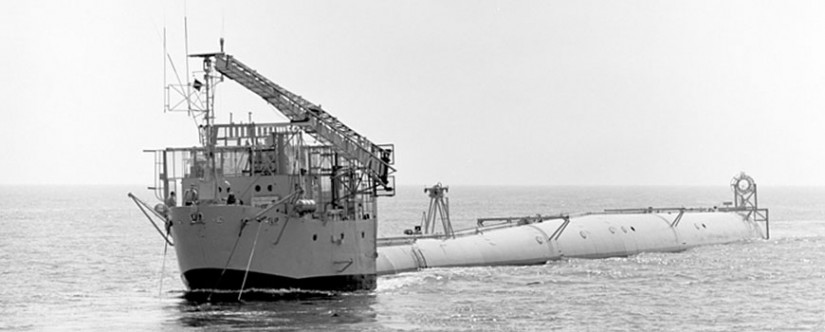
Research Platform FLIP was developed to provide a stable platform to measure fine-scale fluctuations in phase and amplitude of sound waves for the U.S. Navy SUBROC (SUBmarine ROCket) program. One of the major questions concerned bearing accuracy obtained acoustically out to convergence-zone ranges. Horizontal temperature/salinity gradients in the ocean could introduce bearing errors in the volume of the ocean, and sloping bottoms could do the same for acoustic paths that interacted with the bottom. The Navy needed precise measurements to determine the effect of environmental gradients and fluctuations.
In the late 1950s, F.N. Spiess and F.H. Fisher embarked on experimental work to address these problems with Spiess attacking the effect of bottom topography and Fisher attacking the effect of horizontal gradients and fluctuations on bearing accuracy.
Fisher initially used the research submarine USS BAYA (AGSS 318) to make such measurements, piggybacking on research cruises with Frank Hale and Henry Westfall of the US Navy Electronics Laboratory (NEL). After a few cruises, it became clear that the submarine was not a satisfactory platform for this work, even though it had hydrophone booms with a 100-foot span. There was no way to obtain either an optical or electromagnetic-bearing reference in a satisfactory manner at periscope depth or at the desired 300-foot depth needed for separating acoustic multipaths. Even at the 300-foot depth, wave-action effects caused sufficient yawing motion of a submarine to limit measurements of bearing fluctuations in acoustic propagation.
Fisher described these problems to Spiess in January, 1960. Spiess mentioned that Allyn Vine of the Woods Hole Oceanographic Institution had suggested upending a submarine to make a stable platform. Allyn Vine got this idea from observing how stable a navy mop floated in choppy water; that is, the stability of a long, narrow, buoyant object floating in rough water could make it possible to make simultaneously bearing measurements in deep water and compare them with optical or other signals above the water. This interchange resulted in the development of the Research Platform FLIP (FLoating Instrument Platform).
Spiess and Fisher determined that it would not be possible to convert a submarine to a vertical platform and that it would be better to start from scratch. To measure bearing accuracy and the fine-scale fluctuations in bearing (phase difference) and amplitude of sound waves due to inhomogeneities in the ocean such as thermal microstructure and internal waves, a manned spar buoy was proposed as an ideal platform to make such measurements.
The original requirements established for the platform were:
- should have a 300-foot draft to mount hydrophones;
- be acoustically quiet (this led to the requirement that the hull should be completely flooded in the region near the hydrophones to avoid acoustic reflections.);
- have a high degree of torsional rigidity so the position of hydrophones at the 300-foot depth would be known with respect to an optical benchmark in the laboratory above water;
- have an electronics laboratory above the surface from which visual, radio, and radar contact could be maintained with a surface ship; and
- be capable of being berthed at a pier where the draft might be as shallow as 15-feet.
Extensive model studies with different 1/10 scale model configurations were conducted by Fisher to work out the flipping operation. The idea was to simply flood tanks by opening valves to vent the control tanks. These studies led to the need for a hard tank that could withstand the full differential pressure during the flipping operation in order to prevent plunging that occurred when the tanks were allowed to flood freely. By dividing one hard tank into top and bottom sections and adding ballast in the horizontal keel, it was possible to ensure a safe flipping operation.
MPL proceeded to design, conduct model tests and supervise the construction of FLIP, with the assistance of commercial naval architects L. R. Glosten and Associates of Seattle, Washington. FLIP was built in just six months and on June 22, 1962, the full-scale FLIP was launched at the Gunderson Brothers Engineering Corporation yard in Portland, Oregon. Cdr. Earl D. Bronson, USN (ret.), supervised construction and developed the operating techniques. Total initial construction cost was under $600,000.
On July 23, 1962, FLIP was tested for the first time in the Dabob Bay area of the Hood Canal in Washington state on the Navy tracking range. After successfully completing trials of the flipping operation, it was towed to San Diego to commence operations in September 1962.
Many years of operations have included many deployments in the Pacific as far as Hawaii and one deployment to the Atlantic. While originally intended for acoustic research, it has become a versatile platform for research in upper-ocean physical oceanography, meteorology, geophysics, and biology.
Maintenance
In 1994, The Office of Naval Research funded a major phased Maintenance Availability of FLIP. The FLIP Maintenance Availability commenced at the Campbell Shipyard, San Diego, California, on 12 December 1994 and was officially concluded with the completion of a successful sea trial 18-19 January 1996. The Maintenance Availability was conducted in phases, with FLIP supporting research operations between maintenance phases.
During planning for the Maintenance Availability, priorities were established for the accomplishment of repairs, upgrades and maintenance. The established priorities were; structural repairs, safety requirements, upgrades to meet Federal and State regulations, habitability improvements and material reliability. The established priorities were successfully met.
Structural deficiencies reported by Carderock NSWC engineers following a 1993 inspection were corrected with repairs to the interior hull structure, replacement of exterior deck sections and replacement of six sea chests as well as numerous sections of interior air and water piping.
Safety was significantly increased with a major electrical upgrade, installation of an escape hatch from tank 10, boom and winch repairs, installation of a machinery monitoring system, fire main system and a reliable fathometer system. FLIP was brought into compliance with existing regulations with the installation of an approved sanitation system, fire main system, machinery monitoring system, general announcing system and the removal of wooden structures throughout the platform. Material reliability was enhanced with the overhaul of all engines and generators, overhaul of the air compressors, overhaul of the air-conditioning system, replacement of the radar and fathometer, overhaul of all valves and piping systems and replacement of the water-maker.
Habitability improvements included all new galley equipment, new bunks with Coast Guard approved mattresses, replacement of all wooden lockers with light colored aluminum lockers, new deck tile and new improved insulation in all living compartments.
Following the completion of the Maintenance Availability in 1996, FLIP was a safer, more efficient platform from which to conduct oceanographic research. Most importantly, though FLIP remains an uninspected research platform, FLIP now meets major Coast Guard regulations for ocean-going platforms. With the existing aggressive continuing preventative maintenance program, the operational life of FLIP has been extended for an indefinite period.
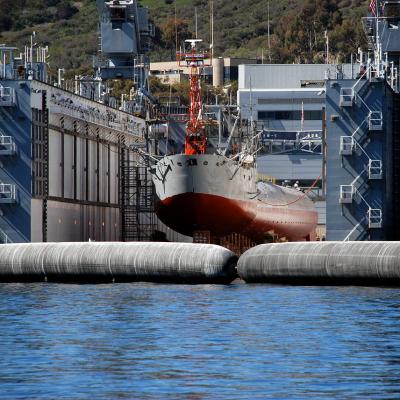
Since completion of the major Maintenance Availability in 1996, an aggressive inspection and preventative maintenance program has been in place, including annual tank inspections and overhaul of the ballast tanks. The preventative maintenance program has been successful in maintaining FLIP in a high state of material readiness. FLIP underwent routine dry dockings in the Navy floating dry dock USS ARCO ARDM 5, in 2001, 2003, 2006, 2010.
The most recent dry docking occurred from June 18 to July 18, 2013. During the 2010 dry docking, FLIP underwent a detailed material inspection, performed by representatives of Glosten Associates Naval Architects & Marine Engineers Seattle, Washington, including taking hull thickness reading throughout the hull, that found FLIP in excellent material condition and able to continue supporting oceanographic research.
50th Anniversary
With special guests onboard, on June 30, 2013, FLIP got underway and proceeded to an area 20 miles west of San Diego for a ceremonial flip. It was flip number 381 of FLIP's research career.
- R/V Sally Ride
-
R/V Roger Revelle
-
Handbook
- Section 1: Welcome Aboard
- Section 2: Specifications
- Section 3: Vessel Layout Description
- Section 4: Ship's and Scientific Equipment Description
- Section 5: Technical Services and Special Equipment
- Section 6: Navigation and Communications Capability
- Section 7: Safety
- Section 8: Ship Organization
- Section 9: Scientific Berthing Plan
- Specifications
- Schematic Drawings
- Berthing Plan
- Scientific Equipment
- Major Shipboard Equipment
-
Handbook
- R/V Robert Gordon Sproul
- R/V Bob and Betty Beyster
- Emeritus: R/V Melville
- Emeritus: R/V New Horizon
- Research Platform FLIP (FLoating Instrument Platform)
- Preventing harassment and discrimination
- Alcohol and illegal drugs: Zero tolerance
- Departure & arrival times
- Pregnancy and Lactation at Sea
- Accommodating Disabilities
- Minimum Age At Sea
- Isotope Use on Scripps Ships
- Geophysical survey requirements in California waters
- Export controls and compliance
- Scientific shipments to Scripps vessels
- Ship to Shore Communications
- Internet use policy
- Winch and Wire Regulations
- Ship Usage Rates
- Data and Sample Distribution Policy
- Stable Isotopes on SIO Ships
- Carryforward of Ship Time
- Using non-UNOLS vessels
- Transportation Worker's Identification Credential (TWIC)
- Naval Clearances
- Notice to mariners
- Volunteering Aboard Scripps Ships
- USCG Rules for Buoys